QUALITY ASSURANCE AND QUALITY CONTROLL MANAGER
Seven Dragons Food Galore Inc.
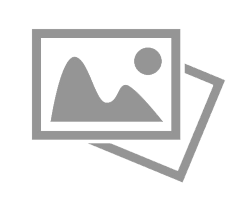
The Quality Assurance and Quality Control (QA&QC) Manager oversees the facility's strategies, objectives and operational status to ensure high quality processes and products. He/She reviews quality testing policies and procedures to ensure that regulatory standards in food manufacturing are followed.
He/She is familiar with good laboratory practices (GLPs) and good manufacturing practices (GMPs). He/She is also familiar with regulatory requirements and guidelines in food safety management and control, such as ISO standards and Hazards and Critical Control Points (HACCP) system. He/She oversees audits and leads investigations into major quality deviations to determine root causes. He/She advises on improved processes to ensure quality standards. He/She possesses strong leadership skills to guide work activities and to help team members to develop their skills in his/her department. He/She has advanced problem-solving skills and is able to make effective decisions.
- Convey data trends, results and potential implications of quality control (QC) data to stakeholders.
- Design quality assurance (QA) policies to prevent issues leading to poor product quality.
- Determine extent of the manufacturing plant's control over quality deviations.
- Develop the organisation's quality testing policy in alignment with regulatory standards.
- Devise an operational excellence model for investigations.
- Devise an operational excellence model for laboratory work based on industry and good laboratory practices (GLPs).
- Establish operational, analytical and documentation standards aligned with industry best practices.
- Establish plans for testing of products, materials and packaging.
- Evaluate the impact of process deviations on operations and the need for corrective and preventative actions (CAPAs).
- Introduce industry best practices and trends in quality inspection and testing methods.
- Oversee QC tasks, ensuring proper documentation of records and review of reports submitted to regulatory authorities.
- Oversee investigations into major process deviations to determine possible reasons.
- Provide expertise on determining the optimal calibration standards for laboratory equipment operation.
- Review and approve standard operating procedures (SOPs) and plans, ensuring alignment with regulations, guidelines and policies.
- Review and make recommendations to address issues identified from the testing activities.
- Review audit results and the proposed changes to procedures.
- Review product and process quality metric reports.
- Translate audit policies into procedures and checks to be followed.
How to apply
To apply for this job you need to authorize on our website. If you don't have an account yet, please register.
Post a resumeSimilar jobs
HR & ADMIN MANAGER
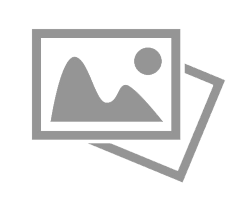
QA Admin
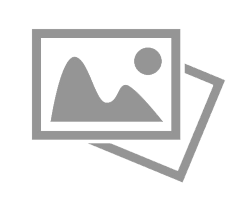
TRUCK DRIVER
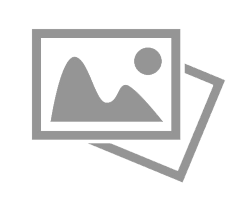